One of the areas we focus on in Building Analytics is energy modeling. It is a term that is used early and often – as well as fast and loose – when discussing sustainability aspects of proposed and existing buildings. Some people involved in such discussions think it is a quick and easy check that can be done in an afternoon. Others say it is an arduous effort that takes weeks or months to complete.
Purpose
It helps to recall the purpose of an energy model. If all you are looking for is the creation of a ballpark figure of merit, such as Energy Usage Intensity (EUI), for entry into the EnergyStar Portfolio Manager, then a quick whole building survey may suffice – and you may even generate that figure yourself. However, the by far greater value of an energy model is to serve as a guide in creating a living roadmap towards reduction of a building’s operating cost. In particular, the crowning achievement of a proper model is the matching of the model’s results to the building’s electricity, natural gas and water bills – the “calibration” of the model. Subsequently, targeted modifications to the model can point out a path towards cost reductions with justifiable confidence.
Process
The key aspects of an energy model include site (e.g. orientation, weather), footprint, envelope and occupancy, as well as lighting, equipment (e.g. office, kitchen), systems (e.g. HVAC) and their controls. It is indeed fairly easy to combine site and high level footprint information with some coarse assumptions about the remaining aspects and come up with a EUI figure. However, to arrive at a true energy model, low level footprint information is required and must be combined with detailed envelope, occupancy, lighting, equipment, system and controls information. It is quite an involved process to use drawings, schedules and submittals to track down the nature of walls, windows, doors, floors, roofs, people count and activity, fixtures, computers, pumps, chillers, fans, air handlers and the like. Fold in the electricity, natural gas and water rate structures, and energy model calibration quickly turns into a serious project requiring intense collaboration among the engineer, architect, operator and/or owner.
Payoff
Consider a “typical” building with a site Energy Usage Intensity (EUI) of 100 kBTU/ft2/y and a gross floor area of 50,000 ft2. If all this energy were electricity purchased at a nominal rate of $0.10/kWh, this would represent utility cost of $146,536/y. If it were natural gas purchased at a nominal rate of $1.25/ccf, it would represent utility cost of $60,916. Split the difference and call it $103,726/y of annual utility cost, not even counting water. Thus, a 10% to 20% reduction may yield savings of $10,373/y to $20,745/y. Over the 25 year to 50 year life of the building, those savings may amount to between $259,315 and $1,037,261.
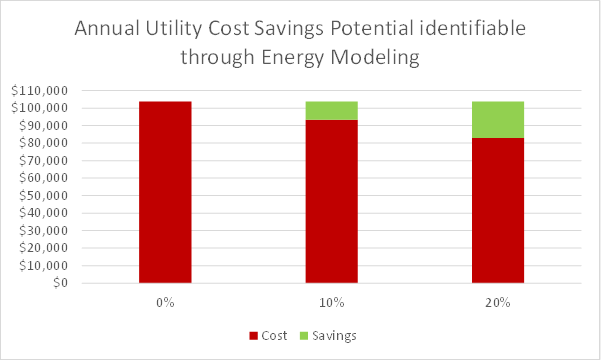
Whether you are realizing a proposed building or upgrading an existing building, don’t leave realizing those savings to chance – implement a true energy model. You cannot improve on what you don’t analyze, and you will not achieve maximum cost reduction if you do not know what knobs to turn in the analysis. It is best to involve a professional engineer to help you maximize the return in investment in an energy model.
By Matt Koch, PhD, PE – Director of Building Analytics